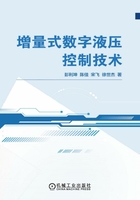
2.2 增量式数字阀建模
2.2.1 数学模型
由增量式数字滑阀的工作原理可知,由于采用螺旋传动结构,滑阀阀芯同时存在旋转和平动两种运动状态,阀芯平动是滑阀阀杆与丝杠螺母的相对旋转运动复合而成的。建模时可将步进电动机-减速机-滑阀阀芯以及步进电动机-减速机-丝杠螺母间的连接视为刚性连接,将阀芯的旋转和平动分开考虑,依次建立相应的数学模型。
1.步进电动机及阀芯旋转数学模型
设输入步进电动机驱动器的脉冲数为N,考虑到输入脉冲的方向性,重新定义脉冲数为矢量,以N的正负代表脉冲方向,即N>0时,输入为正向脉冲,步进电动机正转;而N<0时,输入为反向脉冲,步进电动机反转。步进电动机转子轴实际输出角位移为θ,则步进电动机的数学模型可表示为
式中,θm为细分后步进电动机指令角位移;θs为步进电动机固有步距角;ns为驱动细分数;Te为步进电动机的输出转矩;Tm为最大静转矩;Zr为转子齿数;δθ为旋转电磁场与转子角位移偏差;Jr为转子转动惯量;Be为转子黏性阻尼系数;TL为负载转矩。
设步进电动机转子轴端减速机传动比为is,则传动至滑阀阀芯的角位移为θ/is。设滑阀阀芯旋转的驱动力矩为T,则阀芯旋转动力学方程为
式中,Jm为阀芯等效转动惯量;Bm为阀芯等效旋转阻尼系数;Ts为阀芯旋转综合阻力矩,包含摩擦转矩和阀芯轴向合力产生的阻力矩。
为简化数字滑阀电-机转换部件的数学模型,将阀芯旋转运动等效折算到步进电动机转子轴上。由于阀芯旋转是步进电动机的主要负载,可认为TL≈T/is,故得到
式中,J为折算到步进电动机转子轴上的数字滑阀综合转动惯量,J=Jr+Jm/i2s;B为折算到步进电动机转子轴上的数字滑阀综合黏性阻尼系数,B=Be+Bm/i2s。
联合式(2-1)和式(2-3),可得
由于δθ较小,近似有sinδθ≈δθ,式(2-4)可化简为
对式(2-4)进行拉氏变换,整理后得到步进电动机输出转角传递函数为
2.阀芯平动及反馈环节数学模型
数字阀阀口开度是各机构复合运动的结果,对于双步进电动机数字阀而言,阀芯在主动步进电动机的带动下旋转,其角位移θd在螺杆螺母副的作用下转换为阀芯(即螺杆)的输入位移xin,阀口一旦打开,活塞将产生位移xp,此时位移传感器将产生反馈脉冲,进而驱动反馈步进电动机带动阀芯螺母同向旋转,该螺母的角位移θf在螺杆螺母副的作用下转化为阀芯(即螺杆)的反馈位移xf,最终阀芯的反馈位移xf和输入位移xin合成阀芯平动的绝对位移xv(即阀口开度),因此可得阀芯平动运动方程
式中,xv为阀口开度;xin为阀芯输入位移;xf为阀芯反馈位移,t1为阀芯轴端螺杆螺母导程。
由于驱动步进电动机和反馈步进电动机型号相同,且阀芯和螺母套的工作状况相似,故式(2-6)既可用作驱动电动机的模型,也可用作反馈电动机的模型。若式(2-6)为驱动步进电动机的模型时,只需令
由于作为反馈元件的脉冲输出型位移传感器(一般为光电编码器)的固有频率要远远高于液压伺服系统的固有频率,因此位移传感器的数学模型可认为是一个比例环节,其输入为液压缸活塞杆位移,输出量为反馈脉冲数。此时,若式(2-6)为反馈步进电动机模型时,只需令
式(2-8)、式(2-9)中,θd、θf分别为驱动电动机和反馈电动机的角位移;Nin、Nf分别为输入脉冲数和反馈脉冲数;nsin、nsf分别为驱动电动机和反馈电动机的驱动器细分数;xp为液压缸活塞位移;xr为位移传感器的分辨率。
若位移传感器采用旋转型光电编码器,通过滚珠丝杠等传动机构将液压缸活塞的直线位移转化为旋转角位移,还需考虑其转化关系。设旋转编码器角位移分辨率为θxr,滚珠丝杠导程为t2,则
对于单步进电动机数字阀,由于只有一个驱动步进电动机,阀芯螺母固定,反馈信号直接作用于步进驱动电动机,因此阀芯平动运动方程可简化为
利用步进电动机的数学模型时,可令
从而构建简单的基于增量式数字阀的闭环反馈控制液压伺服系统。
2.2.2 AMESim模型
液压阀的控制特性只有在完整的液压控制回路或系统中才能体现,要研究增量式数字阀的控制特性,就必须构建相对完整的增量式数字阀控液压伺服系统。为重点关注增量式数字阀的阀芯特性,并尽可能地在保证仿真精度的同时降低建模难度和复杂程度,提高仿真效率,下面利用AMESim软件建立增量式数字阀控液压系统的仿真模型。AMESim是多学科的建模仿真平台,具有友好的图形化界面,使用户可以在完整的应用库中选择需要的模块来构建复杂系统的模型并能方便地进行仿真和优化分析,便于工程技术人员掌握,非常适用于机械和液压仿真。增量式数字阀控液压系统的AMESim仿真模型如图2-11所示。主要由三部分组成:油源模型、阀控缸模型和反馈机构模型。油源模型主要使用AMESim液压库(Hydraulic)中的模块搭建完成;阀控缸模型主要使用HCD库(Hydraulic Component Design)中的模块搭建完成;反馈机构模型主要使用机械库(Mechanical)中的模块搭建完成。
1.供油系统模型
供油系统模型如图2-12所示,该系统主要由交流伺服电动机、叶片泵、溢流阀、过滤器、蓄能器和油箱组成,主要功能是实现增量式数字阀控液压伺服系统的可控压力供油。供油系统模型主要使用AMESim中的液压库搭建完成,其中元件2为液压油模型,可以用来定义系统所使用液压油的相关参数,例如:密度、体积弹性模量、黏度、空气含量等,充分考虑油液特性对系统仿真的影响。元件7为溢流阀模型,主要起到安全阀的作用,系统的压力控制主要是通过对交流伺服电动机转速的控制来实现的。
图2-11 增量式数字阀控液压系统的AMESim仿真模型
AMESim仿真平台为每个元件提供了各种复杂等级的仿真模型,用户可以根据各自的独特需要进行选择,表2-1为供油系统各部分元件所选仿真模型及相关参数。
2.阀控非对称缸模型
阀控非对称缸仿真模型如图2-13所示,该模型主要由单出杆液压缸模型和四边滑阀模型两部分组成,模型使用AMES-im的HCD库根据滑阀及单出杆液压缸具体结构原理搭建而成,能够较为详细全面地反映阀控缸的工作状态。
图2-12 供油系统模型
1—蓄能器 2—液压油 3—交流伺服电动机 4—叶片泵 5—过滤器 6—单向阀 7—溢流阀
表2-1 供油系统模型参数
图2-13 阀控非对称缸仿真模型
1—无杆腔 2—活塞 3—可变容积腔 4—阀块 5—负载 6—活塞杆质量 7—有杆腔 8—阀芯质量
图2-13中2为考虑泄漏的活塞模块,模拟液压缸的内泄,3为可变容积腔模块,用来考虑油液的可压缩特性,4为HCD库中的圆柱滑阀阀块,为最基本的液压单元,如图2-13所示利用四个这样的阀块即可搭建出四通圆柱滑阀,6和8分别代表活塞杆和阀芯的质量,该模块除了可以用来考虑质量引起的惯性力之外,还可以对物体运动进行限位及考虑摩擦,模型中丰富的摩擦模型能够较为真实地模拟相对运动物体间的摩擦过程。阀控非对称缸模型参数见表2-2。
表2-2 阀控非对称缸模型参数
3.机械螺纹伺服机构模型
机械螺纹伺服机构模型如图2-14所示,该模型主要使用AMESim机械库中的元件搭建而成,由滚珠丝杠模型(图中右侧部分)和滑动螺旋副模型(图中左侧部分)两部分构成。该机械反馈机构模型的输入为步进电动机角位移θ和滚珠丝杠反馈位移xf,输出为阀芯位移xv。
由于用来做反馈的大导程滚珠丝杠加工困难,本设计采用小导程滚珠丝杠加减速机来代替,模型如图2-14中5和7。滚珠丝杠精度高、摩擦力小,建模时无需很复杂的模型,直接使用机械库中的螺杆螺母机构(即图2-14中7)代替即可。与阀芯相连的滑动螺旋采用的是普通的螺杆螺母机构,存在精度较低、摩擦力较大的问题,因此必须对其螺纹间隙和摩擦特性进行详细的考虑,在模型中体现为模块1和模块4。此外,机械螺纹伺服机构模型中还用到了一个自建的超级元件2,用来实现受力和速度的合成。各模块所使用的模型及参数见表2-3。
图2-14 机械螺纹伺服机构模型
1—双边弹簧阻尼模块 2—超级元件 3—输入信号 4—摩擦块 5—减速齿轮 6—丝杠转动惯量 7—滚珠丝杠
表2-3 反馈机构模型参数